Ways You Can Improve Your Machine Productivity
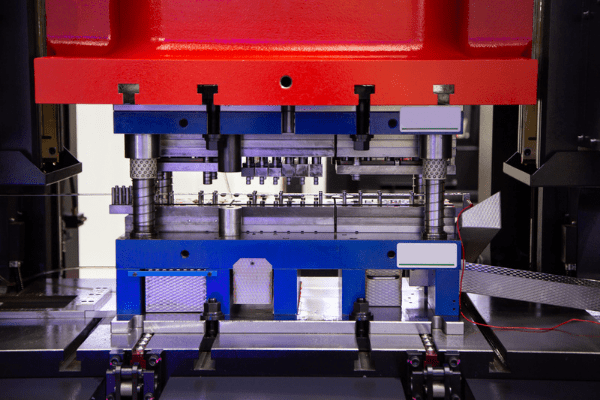
There’s little worse than having a slow production process. You can easily talk to unproductive employees, but slow machines are a different story altogether. Do you know what you call a process that has one thing slowing it down? A bottleneck.
In order to run a successful manufacturing process, you need to look at possible bottlenecks that might be slowing down other processes in your production line. Though bottlenecks are common, they aren’t commonly found unless properly searched for. So, what do you do? You look at all the factors and behaviours that might give you an indication of where the bottleneck is located.
This is especially important if the bottlenecking machine plays a key role in your processes! Watch our video below to find four suggestions on improving your machine productivity and having a smooth-sailing production process.
Look for the bottlenecks
There’s an amazing business manufacturing-related book about the three constraints called The Goal by Goldratt. It was written in the late 80s in the form of a fable. There’s a guy who’s a manufacturing manager having big problems with low productivity. He’s also the leader of the scout troop. One Sunday afternoon he takes his troop out on a hike. The fastest kids of the troop are at the front of the line, the slowest guys at the back.
He stands at the back of the line looking at his scout troop stretched out for over a mile. He’s thinking of ways that he needs to stop that and bring them all back together. So, he has the idea that, rather than the fastest guys at the front who are getting further and further ahead, why not put the slowest guy at the front of the line, to set the pace for the entire troop. Then something amazing happened. The people behind him wanted to go faster, so they took stuff out of the slowest guys backpack so that he could go faster and as a result, they could all go faster.
So, that’s basically the theory for looking for bottlenecks in your factory. If you’ve got a process that’s at full capacity and can’t go any faster, there’s no point spreading your focus around and speeding up other areas of the factory. They’ll get faster and faster, but they’ll have nothing to do because you’ve got an area of the factory that’s a bottleneck that can’t keep up with that.
You should, therefore, base 100 per cent of your effort on, finding the bottlenecks. Look for areas where there’s excess work in progress. Look at places where there’s excess downtime or, an interesting one, where people have got weird workarounds outside of the process, to overcome some of these bottlenecks.
Reduce the Workload of the Bottleneck Assets
Using exactly the same principle of the goal story, look for ways to take stuff out of the “backpack”.
If you’ve got a machine and you’ve identified it as a bottleneck in your process, look to see what the really core things are that only this machine can do. Anything extra, make sure you take it away from that area of your process.
So, if you’ve got any debearing or cleaning processes mixed in there, just take them out. Get someone to manually do that afterwards or buy another cheaper machine to do that before it goes in. If you get them out of the bottleneck area as soon as you possibly can, you might be able to free up an extra 10 or 20 per cent of that machine’s availability, for doing the core function that only that asset and that machine can do.
Look at Machine Upgrades
Once you’ve identified your bottleneck and reduced its workload so it’s only doing essential stuff, what can you do to improve its efficiency even more?
Even in machines that are only two or three years old, sometimes the rate of change in technology means there are much more efficient motors, more efficient methods of cooling or lubrication.
There be some simple upgrades available from the machine manufacturer, to give it an extra five or 10 per cent worth of efficiency. If that’s a bottlenecked area for you, that could mean, an extra 10, 20 per cent output of your product. So, speak to your service engineers for your key machines and see what upgrades are available and what they could give you.
Increasing Capacity
If there aren’t upgrades available, if it’s that bottlenecked area, look at increasing capacity.
If you bought an extra one of those machines, what would that let you do? Would that let you double your output? If it’s a bottlenecked area it should give you a big impact. If you double it, it’s probably not going to be the bottleneck anymore and somewhere else further down the line will become the constraint.
So, just before going down that route, try to get an understanding of what will be the next constraint and the next bottleneck. Decide what actions you can take and what it will cost to get the throughput that you need all along your production line.
Summary
So the four suggestions for improving your machine productivity are:
- Identify what the bottlenecks are in your factory.
- Look at ways to reduce the workload from those critical path assets.
- Speak to your supplier about any upgrades.
- Look at increasing the capacity.
Unleash the Power of Digital Manufacturing
Download our free Digital Transformation Starter Kit to set the gold standard for operational clarity and excellence.