Manufacturing Digital Transformation
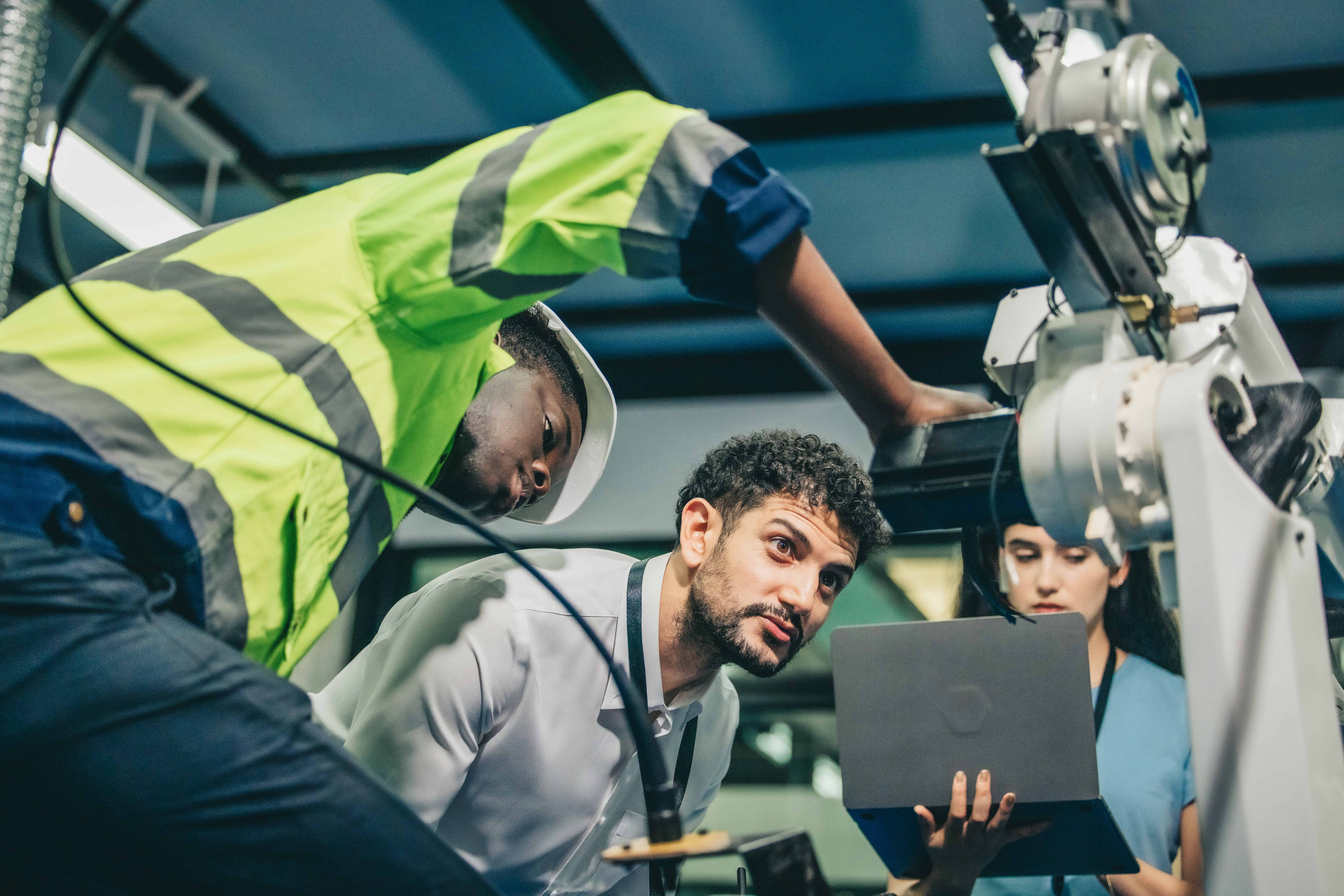
In today’s fast-paced manufacturing world, automotive and aerospace companies face increasing pressure to deliver high-quality products while also improving efficiency and scaling operations. Customers and regulators demand consistent quality, faster turnaround times, and strict compliance with industry standards like TS 16949 and AS9100. At the same time, manufacturers must remain cost-competitive and adapt to digital advancements.
Despite having a skilled workforce and a strong reputation, many manufacturers still struggle with inefficiencies, quality risks, and outdated legacy systems that slow down production, increase waste, and make it difficult to scale.
So, what are the real options for overcoming these challenges?
In this post, we’ll explore three common approaches manufacturers take—incremental adjustments, full system overhauls, and scalable digital transformation—to see which one truly enables sustainable efficiency, quality improvements, and long-term growth.
Download the Smart Factory Blueprint to start simplifying and enhancing your manufacturing operations with practical tools and insights.
Download the Smart Factory Blueprint to start simplifying and enhancing your manufacturing operations with practical tools and insights.
Common Approaches to Addressing Manufacturing Inefficiencies
Option 1: Incremental Adjustments
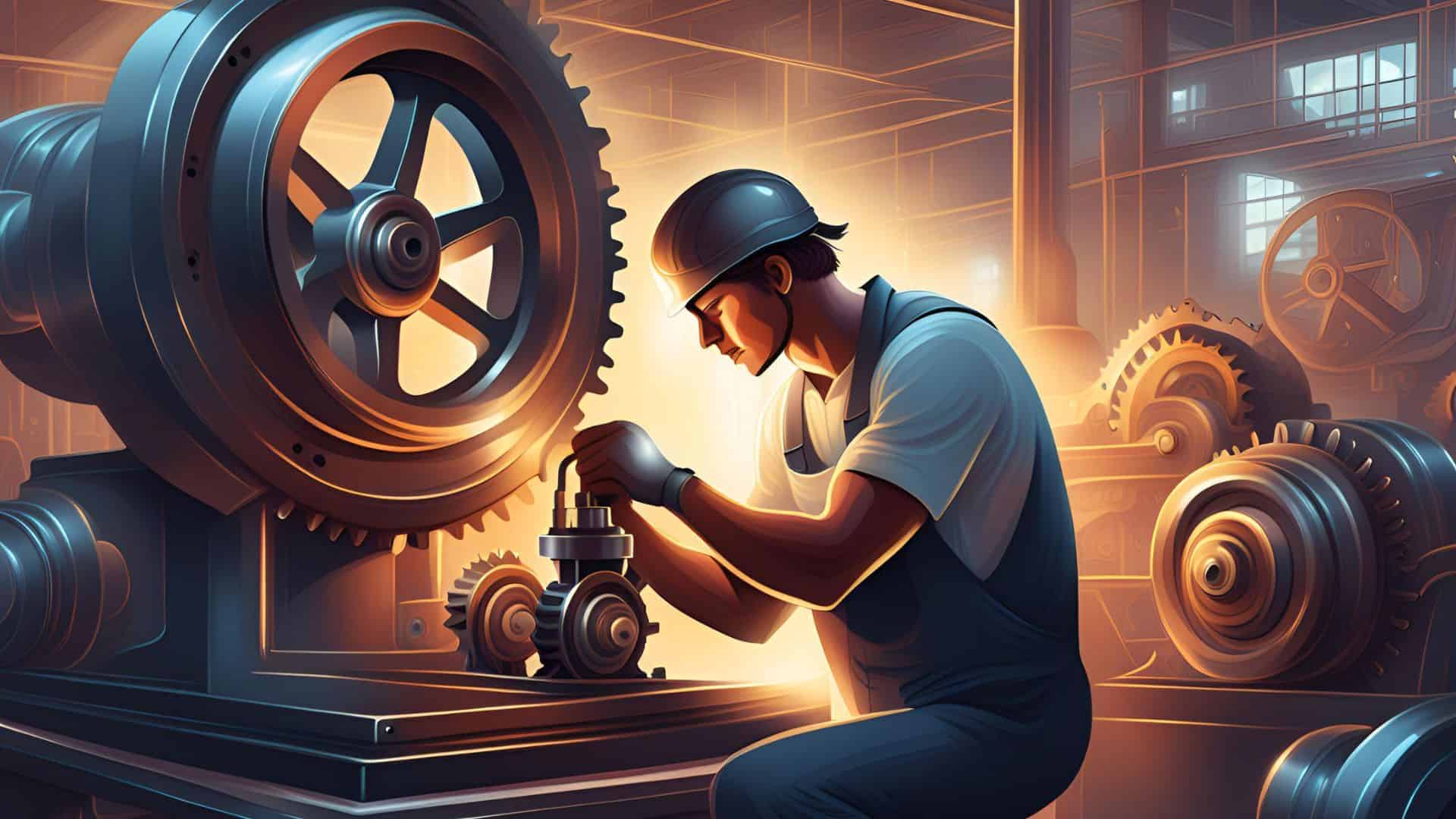
For many manufacturers, the first instinct when facing inefficiencies or quality issues is to tweak existing processes. This approach is often seen as the least disruptive—adjustments can be made gradually, without halting production or requiring significant investment.
Common incremental adjustments include:
✔ Introducing new workforce training programs to improve process adherence.
✔ Adding manual quality checks at key production stages.
✔ Modifying existing workflows to increase efficiency.
✔ Implementing isolated digital tools without full system integration.
While these changes can deliver small wins in the short term, they fail to address the root causes of inefficiencies and quality risks.
Option 1: Incremental Adjustments
Why This Approach Fails:
-
- Doesn’t fix underlying systematic issues – Small tweaks don’t address the bigger challenges manufacturers face, such as lack of process standardisation, poor real-time visibility, and disconnected systems.
-
- Vulnerable to operational risks – Without a structured framework, issues like production delays, quality inconsistencies, and compliance gaps.
-
- Scaling limitations – When demand increases, manufacturers relying on minor adjustments often struggle to maintain efficiency and quality at scale.
Manufacturers that rely solely on incremental adjustments often find themselves stuck in a cycle of firefighting, where short-term fixes provide temporary relief but fail to create lasting improvements. To achieve long-term operational efficiency and quality control, a more structured and scalable approach is needed.
Download the Smart Factory Blueprint to start simplifying and enhancing your manufacturing operations with practical tools and insights.
Common Approaches to Addressing Manufacturing Inefficiencies
Option 2: Full System Overhaul
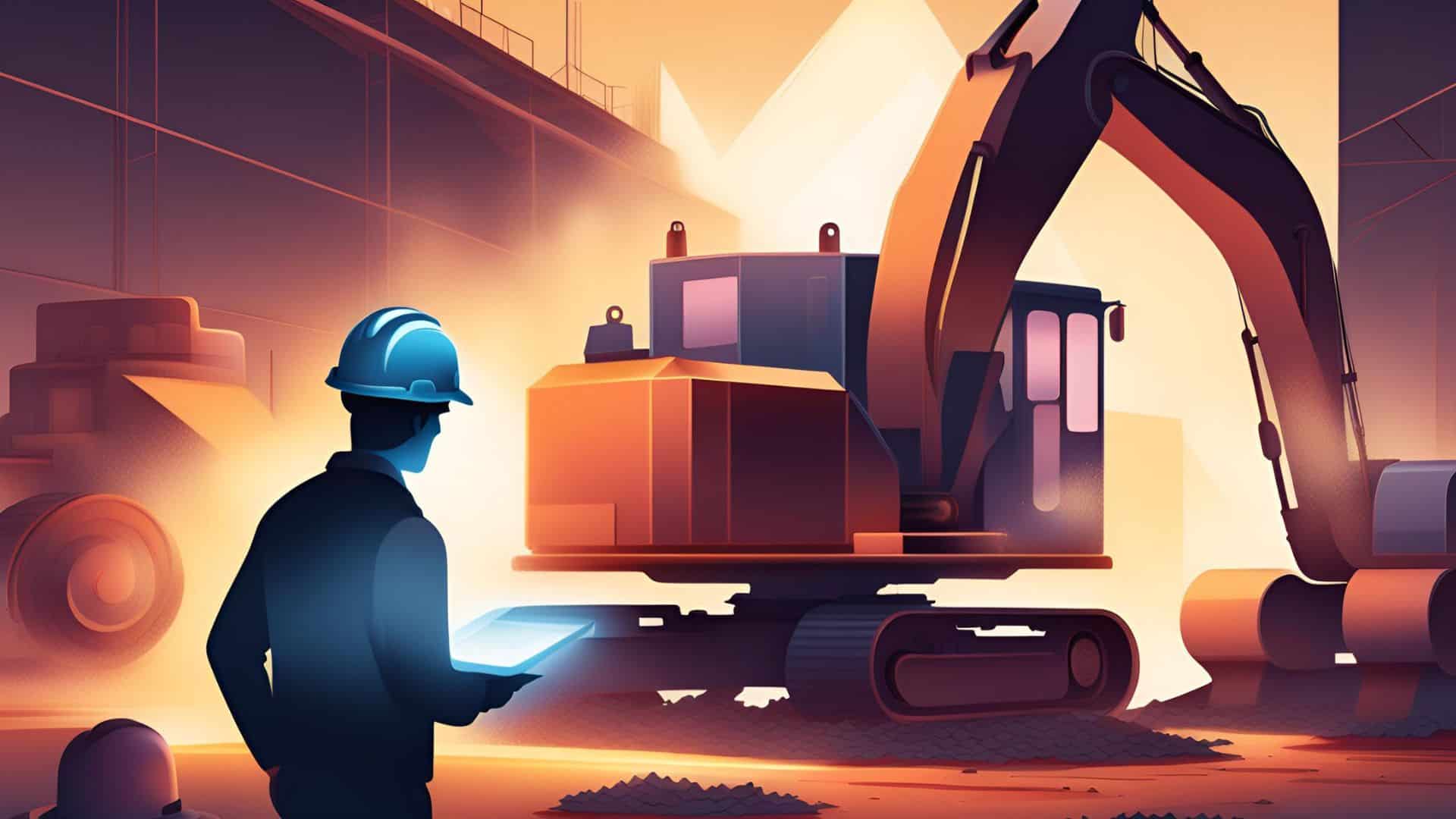
When faced with persistent inefficiencies and outdated systems, some manufacturers take a drastic approach—completely replacing their legacy infrastructure with an entirely new system. The idea behind this strategy is to eliminate inefficiencies at the root and modernize operations with state-of-the-art technology.
At first glance, a full system overhaul seems like the ultimate solution—wiping the slate clean and starting fresh with fully integrated, advanced manufacturing systems. However, the reality is that this approach comes with significant costs, risks, and operational challenges.
The Challenges of a Full System Overhaul
-
-
- High Costs – A complete overhaul requires major upfront investment in new software, hardware, and employee training. Many manufacturers, especially SMEs, find this approach cost-prohibitive.
-
-
-
- Operational Disruptions – Transitioning from legacy systems to a brand-new infrastructure often means downtime, slowed production, and retraining staff, all of which impact efficiency and profitability in the short term.
-
-
-
- Implementation Complexity – Large-scale changes require careful planning, resources, and expertise to execute successfully. Without proper change management, manufacturers risk delays, errors, and resistance from employees adapting to the new systems.
-
-
-
- Uncertain ROI – Even if a company invests heavily in a complete overhaul, the return on investment isn’t guaranteed. If the new system fails to integrate smoothly with existing processes or doesn’t deliver expected improvements, manufacturers can be left worse off than before.
-
Option 2: Full System Overhaul
Why This Isn’t a Realistic Solution for Most Manufacturers
For many manufacturers, a full system overhaul simply isn’t a feasible option. The risks and costs are too high, and the disruption to operations can be overwhelming.
Instead, manufacturers need a practical, scalable alternative—one that allows them to improve efficiency and quality without completely replacing existing systems. This leads us to the third and most effective approach: an integrated scalable digital transformation.
In the next section, we’ll explore how a structured, step-by-step digital transformation strategy enables manufacturers to enhance efficiency, improve quality, and scale operations—without the high costs and risks of a full system overhaul.
Download the Smart Factory Blueprint to start simplifying and enhancing your manufacturing operations with practical tools and insights.
The Best Approach:
Integrated Scalable
Digital Transformation
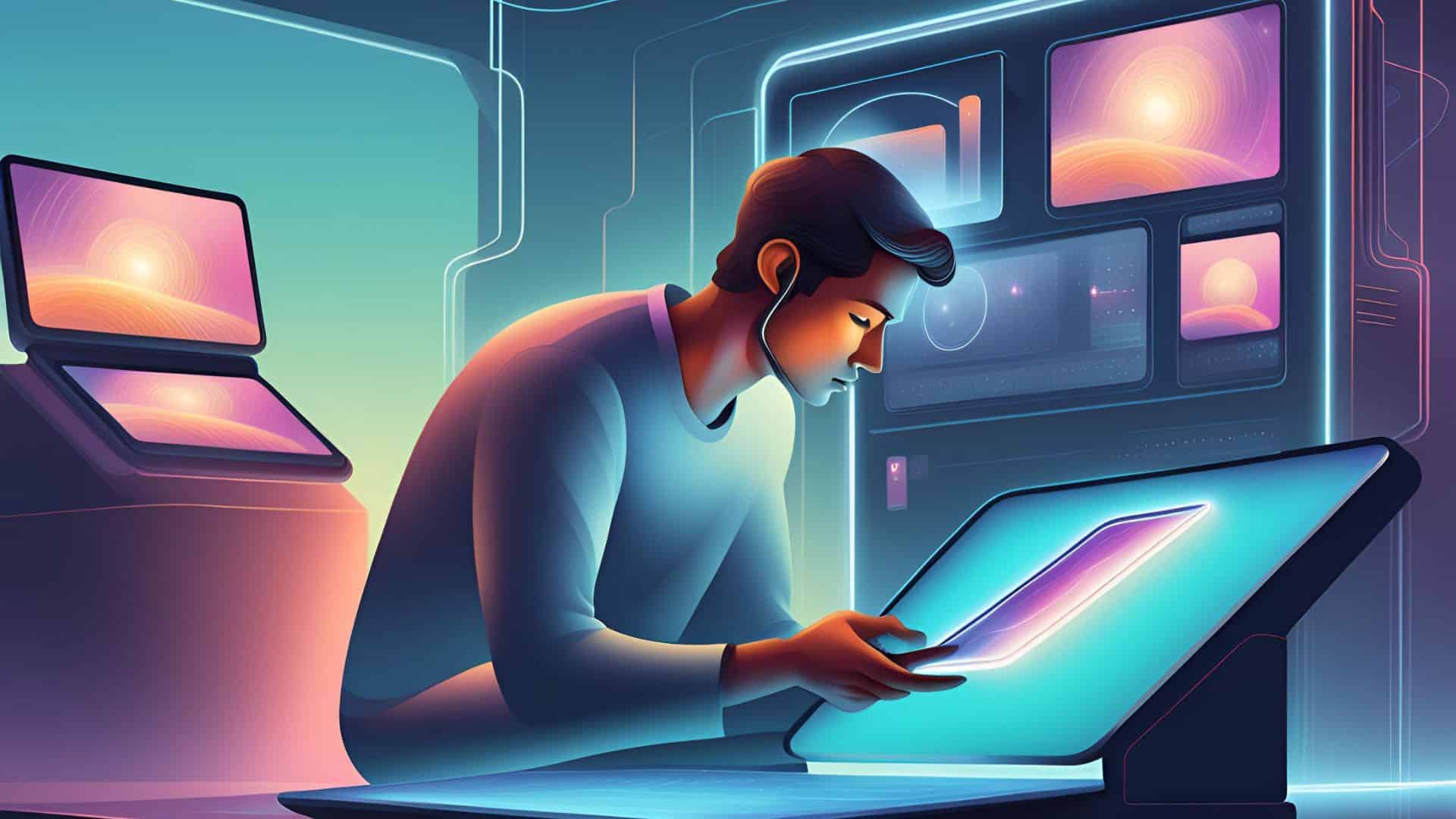
For manufacturers looking to increase efficiency, ensure quality, and scale operations—without the risks of a full system overhaul—the most effective solution is a structured, scalable digital transformation.
Unlike incremental adjustments, which offer only temporary relief, and full system overhauls, which are costly and disruptive, this approach integrates digital tools and lean principles into existing processes—enhancing operations without major disruptions.
How a Structured Digital Transformation Works
This approach focuses on four key pillars that drive efficiency, quality, and scalability:
-
- Lean Principles – Reducing waste, eliminating bottlenecks, and standardising processes to improve operational efficiency.
-
- Embedded Quality Control – Integrating automated quality checkpoints and real-time monitoring to ensure consistent, high-quality production.
-
- Real-Time Data Analytics – Providing instant insights into production performance, allowing manufacturers to make data-driven decisions that improve efficiency and reduce errors.
-
- Continuous Improvement – Creating a scalable system that adapts and evolves over time, driving long-term efficiency and growth.
Why This Approach Works for Manufacturers
✔ Real-Time Decision-Making – Immediate access to production data and quality metrics helps manufacturers respond to issues before they escalate.
✔ Reduces Waste & Inefficiencies – Identifies and eliminates non-value-adding activities, improving cycle times and resource utilisation.
✔ Improves Traceability & Compliance – Meets industry standards like TS 16949 and AS9100, ensuring that products meet strict regulatory requirements.
✔ Scalable, Phased Implementation – Instead of a disruptive overhaul, this strategy allows manufacturers to integrate digital tools step by step, minimising risk while steadily improving operations.
Download the Smart Factory Blueprint to start simplifying and enhancing your manufacturing operations with practical tools and insights.
Conclusion: A Proactive and Scalable Solution
The challenges facing automotive and aerospace manufacturers—rising quality demands, inefficiencies, and legacy system constraints—require a practical, scalable solution. While incremental adjustments provide only temporary fixes and full system overhauls are costly and disruptive, a structured digital transformation offers the best path forward.
By integrating lean principles, real-time analytics, and embedded quality control, manufacturers can:
✔ Reduce inefficiencies without disrupting operations.
✔ Ensure consistent quality while meeting industry standards.
✔ Make data-driven decisions that improve production outcomes.
✔ Scale operations sustainably to support long-term growth.
Instead of patching over inefficiencies or starting from scratch, manufacturers can implement a phased, structured approach that strengthens their existing processes while preparing for the future.
What’s Next?
In the next post, we’ll break down a simple yet powerful 4-step framework that manufacturers can follow to implement a structured digital transformation. This approach ensures they can overcome inefficiencies, improve quality, and scale their operations effectively—without major risk or disruption.
Stay tuned! 🚀
Let’s Talk Tascus
Want to see how Tascus can cut errors,
speed up production, and simplify
compliance in your factory?