4 Steps to Paperless Manufacturing
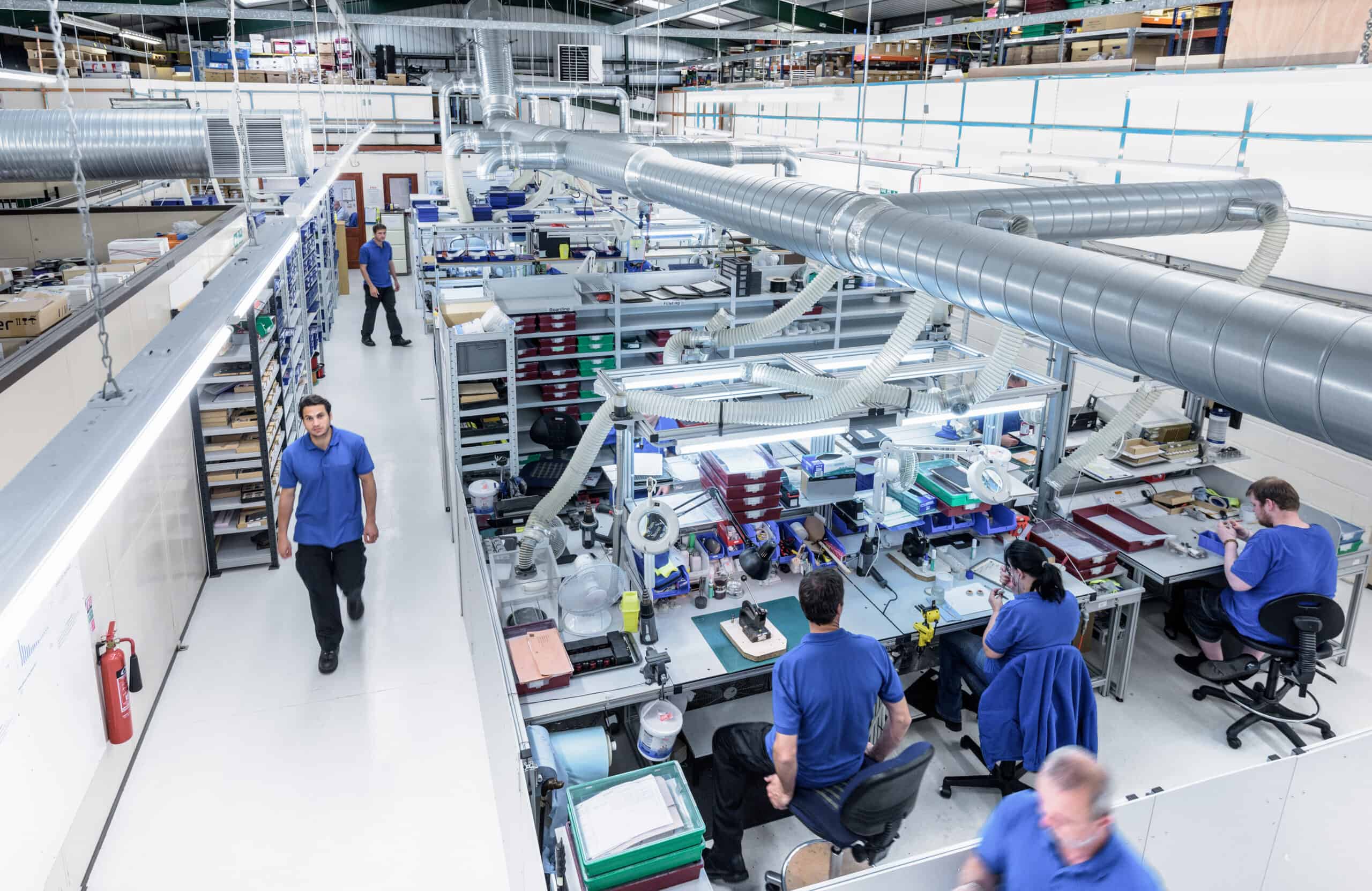
The transition to a paperless manufacturing process is no longer a luxury—it’s a necessity for manufacturers who want to stay competitive. But digital transformation isn’t just about adding new technology. It’s about creating efficient, standardised, and scalable processes that can adapt to changing demands and support long-term growth.
Many manufacturers face challenges such as inefficiencies, inconsistent workflows, and a lack of real-time data visibility, which can make the move to a digital system feel overwhelming.
This is where a structured approach can make all the difference. By following a clear 4-step process—Standardise, Quality Control, Analyse, and Improve—manufacturers can build a high-performing, digitally enabled operation that’s ready to embrace paperless manufacturing.
In this post, we’ll break down these steps, giving you practical insights to make your transition to a paperless and data-driven manufacturing process seamless, efficient, and effective
Download the Smart Factory Blueprint to start simplifying and enhancing your manufacturing operations with practical tools and insights.
Step 1: Standardise
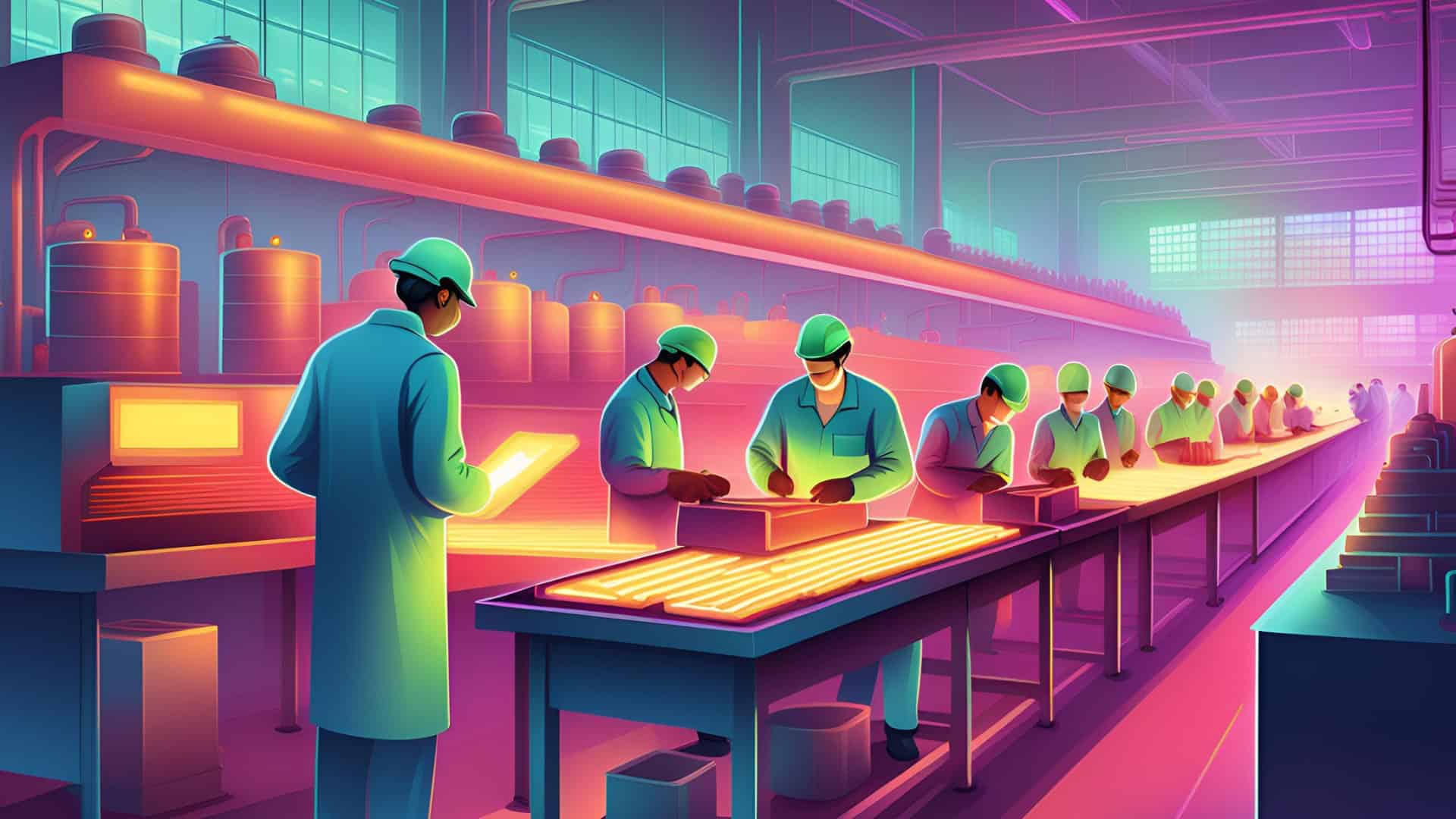
The first step in the paperless manufacturing process is standardisation, which lays the groundwork for a seamless and successful digital transformation. Without a strong foundation, waste, inefficiencies, and process variations can easily disrupt operations, making it harder to achieve consistency and scale effectively.
How can manufacturers standardise their processes?
- Align with lean principles: By focusing on eliminating waste and streamlining workflows, manufacturers can ensure every step adds value.
- Establish repeatable workflows: A clear, consistent baseline for operations ensures that processes are reliable and ready for digitisation.
- Reduce process variation: Standardising ensures that each production step delivers consistent results, which is crucial for tracking and improving efficiency.
When processes are standardised, manufacturers gain clarity and control over their operations, creating a foundation that supports every subsequent step in the transformation.
Why Standardisation Matters:
Standardisation not only eliminates inefficiencies but also provides a solid framework for digital tools to operate efficiently. This ensures that the transition to a paperless system is smooth, scalable, and effective—setting the stage for improved quality control, analytics, and continuous improvement.
Download the Smart Factory Blueprint to start simplifying and enhancing your manufacturing operations with practical tools and insights.
Step 2: Quality Control
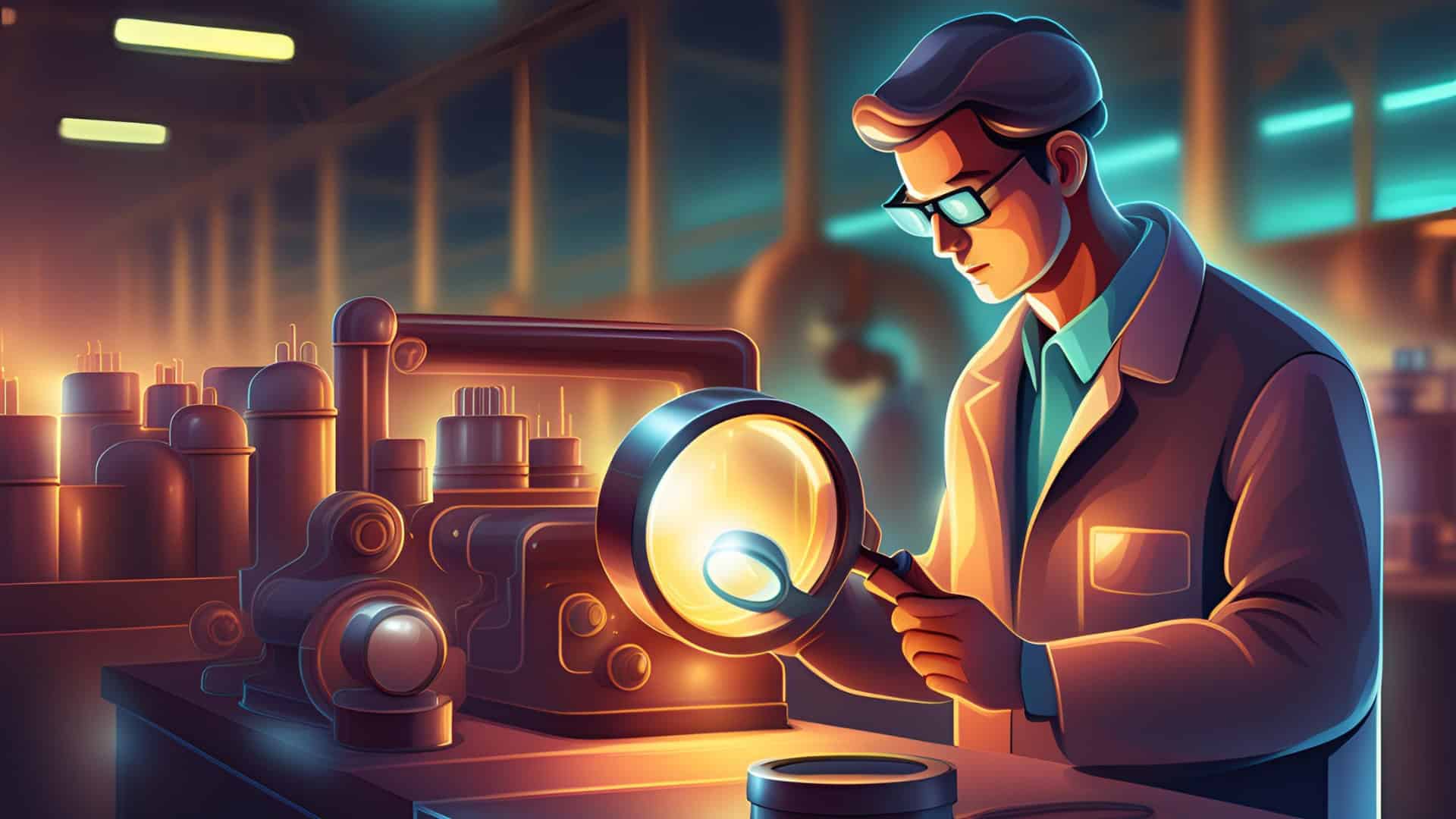
In the journey toward a paperless manufacturing process, quality control plays a pivotal role. Without consistent quality, even the most efficient systems can falter, leading to defects, costly rework, and dissatisfied customers. Embedding precision at every stage of production is key to ensuring that digital transformation delivers measurable results.
How can manufacturers implement better quality control?
- Embed quality checkpoints: Place checkpoints throughout the production process to catch errors early, ensuring problems are addressed before they escalate.
- Digitise quality control: Digital tools allow for real-time error detection and traceability, helping teams monitor processes closely and respond instantly to issues.
- Reduce defects and rework: By identifying and correcting issues at each stage, manufacturers can minimise waste, improve reliability, and save both time and money.
By prioritising quality control, manufacturers can build confidence in their processes, ensuring that every product meets the highest standards.
Why Quality Control Matters:
A robust quality control system doesn’t just enhance product reliability—it also supports the broader goals of a paperless manufacturing process by reducing inefficiencies, boosting customer satisfaction, and lowering production costs. When digitised, quality control becomes a powerful tool for driving consistency and precision.
Download the Smart Factory Blueprint to start simplifying and enhancing your manufacturing operations with practical tools and insights.
Step 3: Analyse
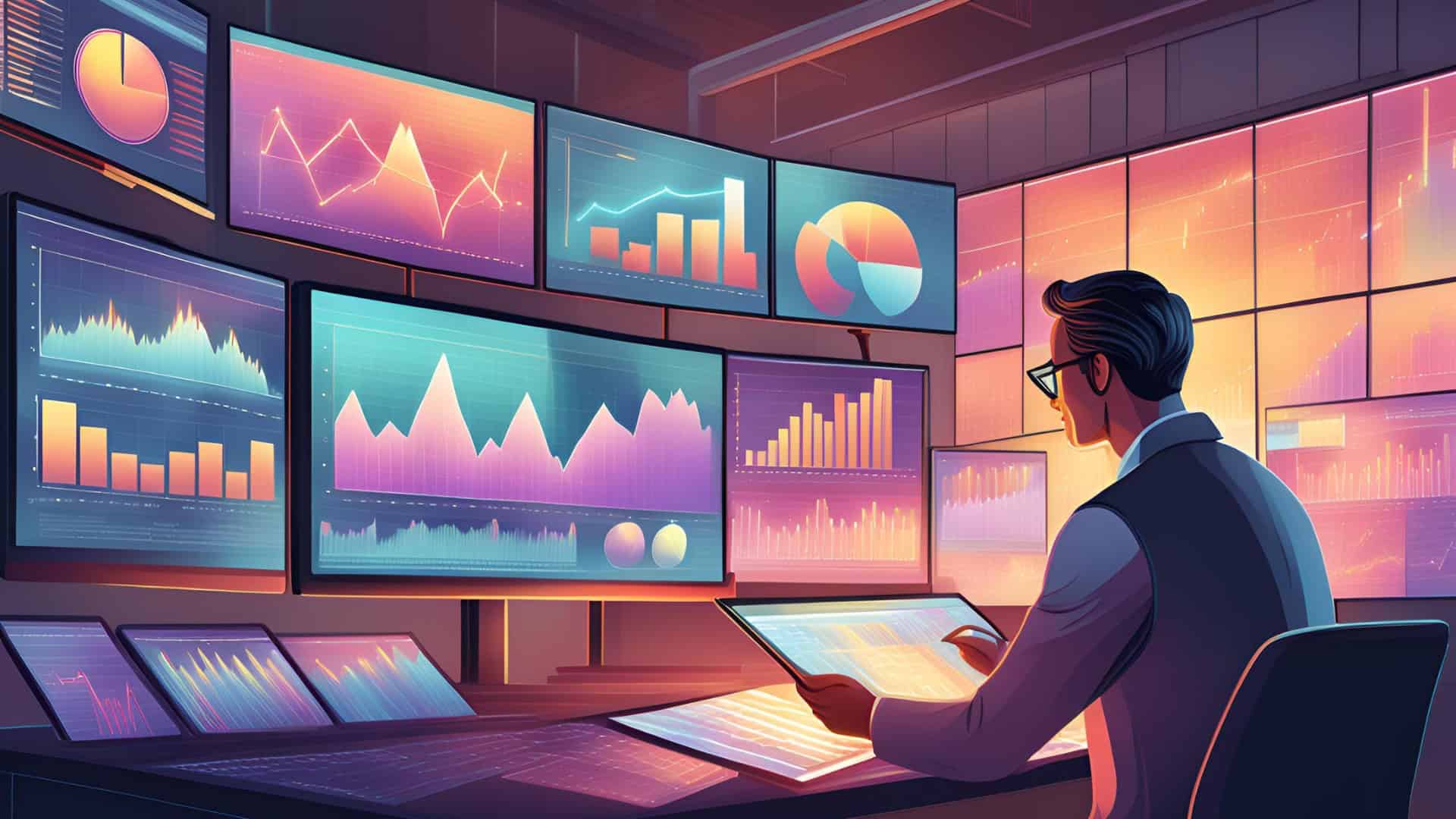
In a paperless manufacturing process, data is the key to making informed decisions and driving continuous improvement. Yet, many manufacturers operate without real-time visibility, which leads to delays, inefficiencies, and missed opportunities for optimisation. By leveraging analytics, manufacturers can turn their production data into actionable insights that drive better outcomes.
How can manufacturers unlock the power of data?
- Integrate real-time analytics: Implement tools that provide immediate insights into production performance, allowing teams to monitor processes and respond to changes as they happen.
- Identify bottlenecks: Use data to spot inefficiencies or disruptions before they escalate, ensuring smoother operations and reduced downtime.
- Make data-driven decisions: Empower production managers with the information they need to continuously refine workflows, improve processes, and boost productivity.
Analytics doesn’t just improve visibility—it transforms the way manufacturers operate, making data an essential tool for smarter, faster decisions.
Why Data Analytics Matters:
Real-time analytics doesn’t just enhance decision-making—it also supports the broader goals of a paperless manufacturing process by enabling teams to act quickly, optimise production, and refine operations using data-driven insights. When digitised, analytics becomes a powerful tool for driving efficiency, precision, and adaptability.
Download the Smart Factory Blueprint to start simplifying and enhancing your manufacturing operations with practical tools and insights.
Step 4: Improve
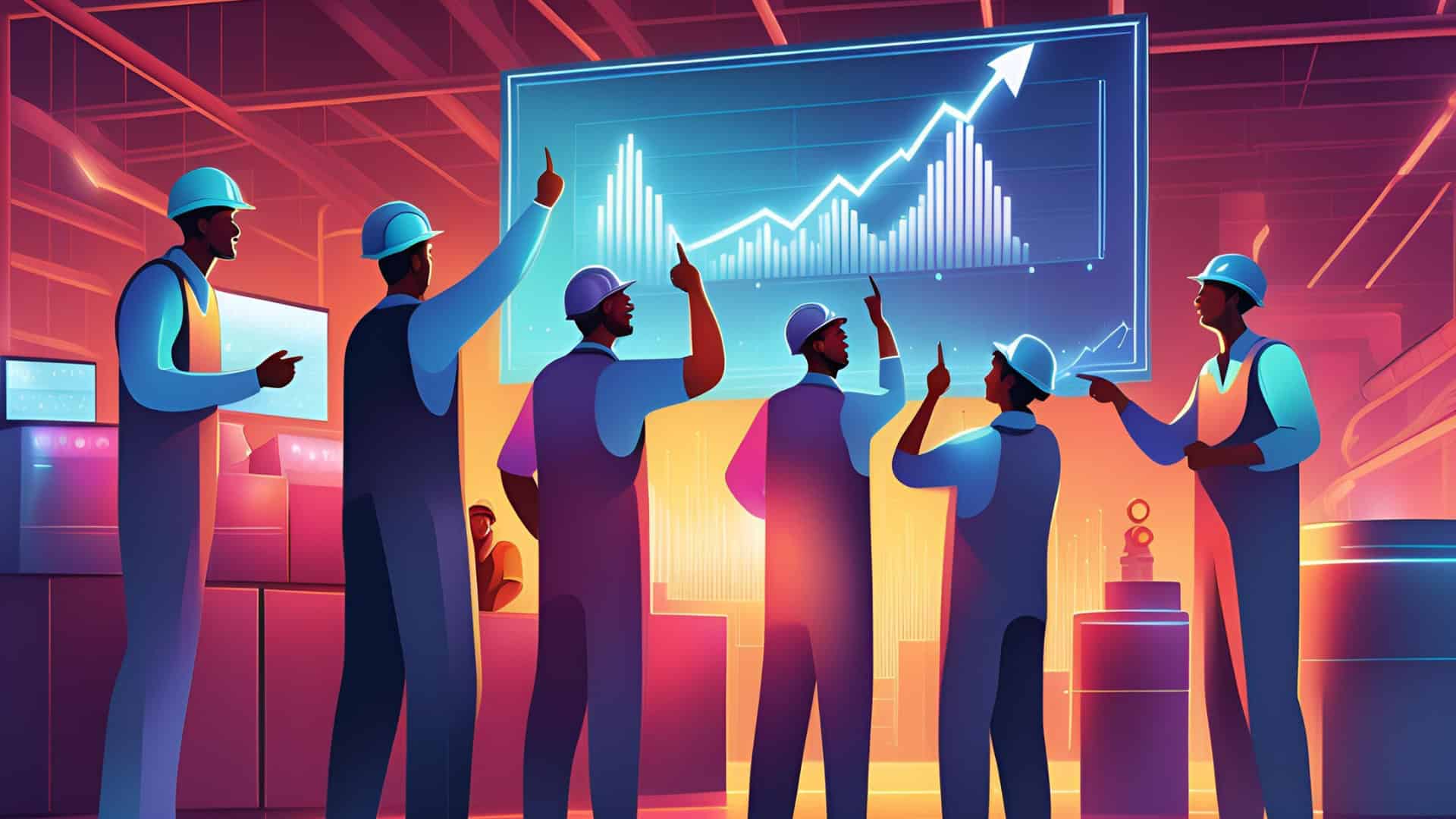
A successful paperless manufacturing process isn’t a one-and-done transformation—it’s an evolving journey. Continuous improvement ensures that manufacturers remain competitive, adaptive, and ready to tackle future challenges. By focusing on incremental gains, businesses can drive efficiency and scalability over the long term.
How can manufacturers foster continuous improvement?
- Create feedback loops: Use real-time performance data to provide actionable insights, helping teams identify areas for improvement and adjust processes accordingly.
- Encourage employee participation: Empower employees to actively contribute by suggesting and implementing improvements, creating a culture of innovation and engagement.
- Refine processes over time: Regularly evaluate workflows and adapt them to meet changing demands, ensuring the business remains agile and scalable.
Continuous improvement turns a digital transformation into a living, evolving process, keeping manufacturers at the forefront of efficiency and innovation.
How can manufacturers unlock the power of data?
- Integrate real-time analytics: Implement tools that provide immediate insights into production performance, allowing teams to monitor processes and respond to changes as they happen.
- Identify bottlenecks: Use data to spot inefficiencies or disruptions before they escalate, ensuring smoother operations and reduced downtime.
- Make data-driven decisions: Empower production managers with the information they need to continuously refine workflows, improve processes, and boost productivity.
Analytics doesn’t just improve visibility—it transforms the way manufacturers operate, making data an essential tool for smarter, faster decisions.
Why Continuous Improvement Matters:
Incorporating continuous improvement into a paperless manufacturing process ensures ongoing efficiency gains, employee engagement in innovation, and long-term scalability, making digital transformation a sustainable success rather than a one-time upgrade. By embedding a culture of continuous improvement, manufacturers can keep their operations dynamic, efficient, and prepared for growth.
Download the Smart Factory Blueprint to start simplifying and enhancing your manufacturing operations with practical tools and insights.
Conclusion
Transitioning to a paperless manufacturing process is no small feat, but with a clear and structured approach, it’s entirely achievable. By following the 4-step process—Standardise, Quality Control, Analyse, and Improve—manufacturers can unlock transformative benefits that position them for long-term success.
This framework provides a roadmap for:
✔ Streamlining operations and eliminating inefficiencies to create more reliable workflows.
✔ Ensuring consistent, high-quality production with real-time monitoring and error detection.
✔ Leveraging data-driven insights to make smarter, faster decisions.
✔ Building a scalable, digital-first manufacturing process that supports adaptability and growth.
By focusing on efficiency, precision, and continuous improvement, manufacturers can create an operation that’s not only more productive but also resilient to future challenges.
📢 What’s Next?
In our next post, we’ll take a deep dive into Step 1: Standardisation, exploring how lean principles can set the stage for a smooth and scalable digital transformation.
Stay tuned for actionable insights to kickstart your paperless journey! 🚀
Let’s Talk Tascus
Want to see how Tascus can cut errors,
speed up production, and simplify
compliance in your factory?