Quality Control in Manufacturing: 4 Steps to Improve Consistency
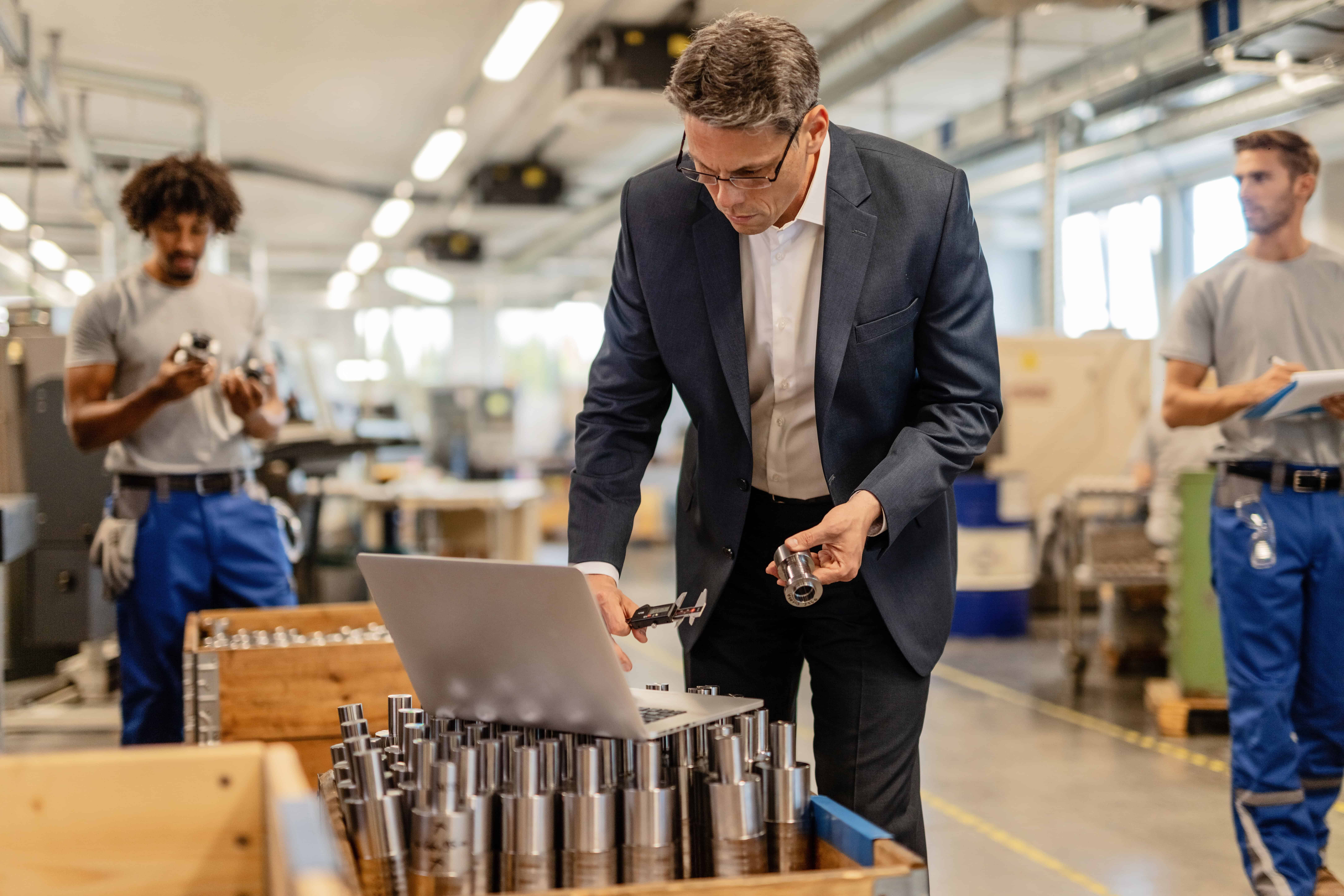
Quality control isn’t a nice-to-have in manufacturing — it’s essential.
Without a structured approach to quality, defects, waste, and unhappy customers can quickly eat into your profits and reputation. Consistency in production is what builds trust with customers and helps your team operate at a high level every day.
If you’ve experienced rework, missed issues, or variability across shifts or sites, you’re not alone. The solution isn’t more end-of-line inspections — it’s building quality control into every stage of production.
In this post, we’ll walk you through a practical 4-step quality control checklist to help you:
-
Reduce defects
-
Improve product consistency
-
Streamline audits
-
Build a quality-first culture
Let’s get into it.
Download the Smart Factory Blueprint to start simplifying and enhancing your manufacturing operations with practical tools and insights.
Step 1: Identify Critical Checkpoints
in Your Quality Control Process
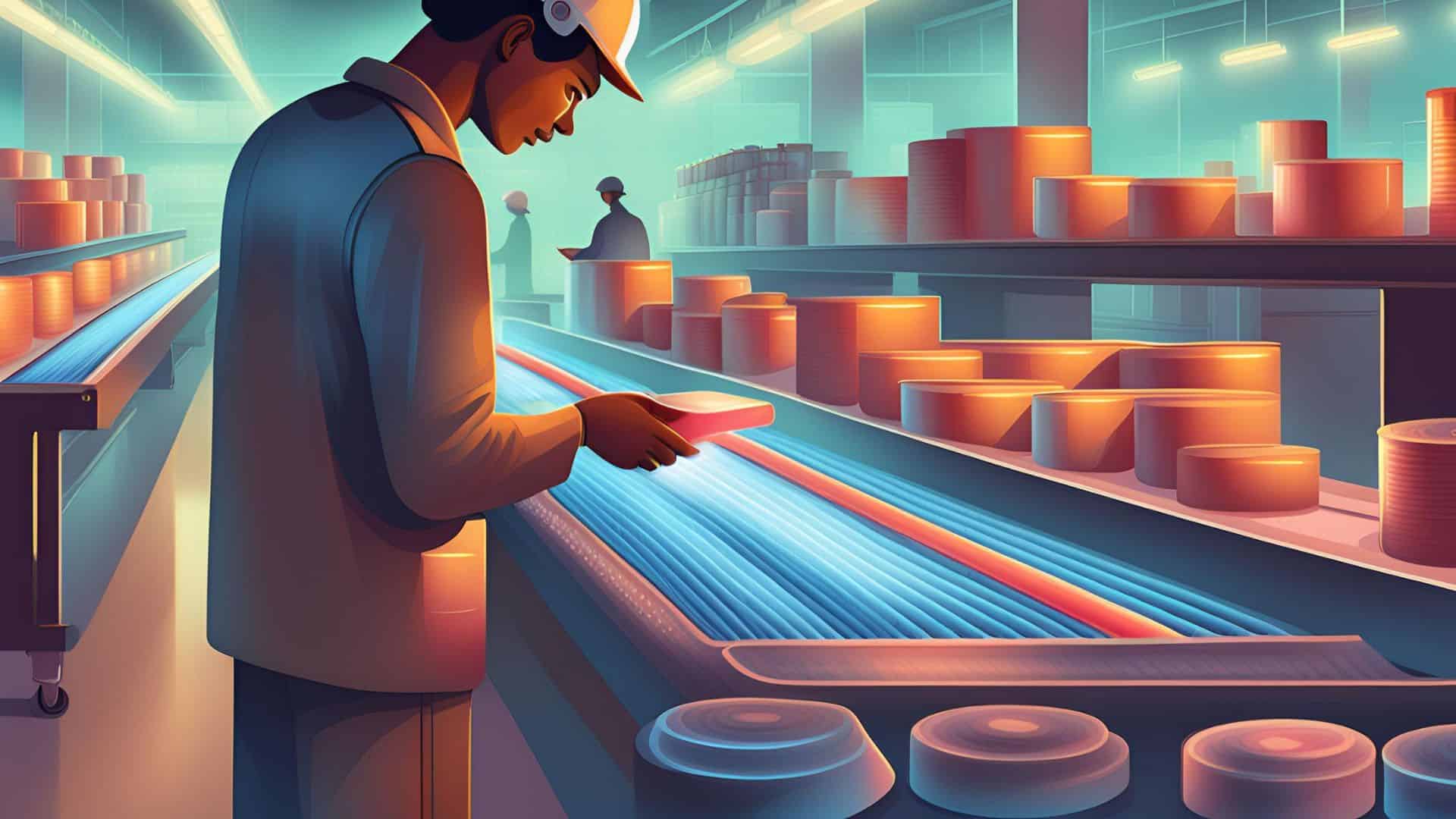
Every production process has points where errors are more likely to occur. These could be transitions between teams, manual operations, or complex assemblies.
Start by mapping out your production flow and highlighting vulnerable stages. Use production data, defect logs, or operator feedback to identify where quality checks would catch the most issues.
The UK Government’s Manufacturing Best Practices and Productivity Report recommends continuous improvement strategies like Lean and Six Sigma to pinpoint bottlenecks and reduce variation.
By defining these critical checkpoints, you can catch problems early and reduce the knock-on effect of passing defects down the line.
Download the Smart Factory Blueprint to start simplifying and enhancing your manufacturing operations with practical tools and insights.
Step 2: Define Clear Quality Control
Standards for Manufacturing Consistency
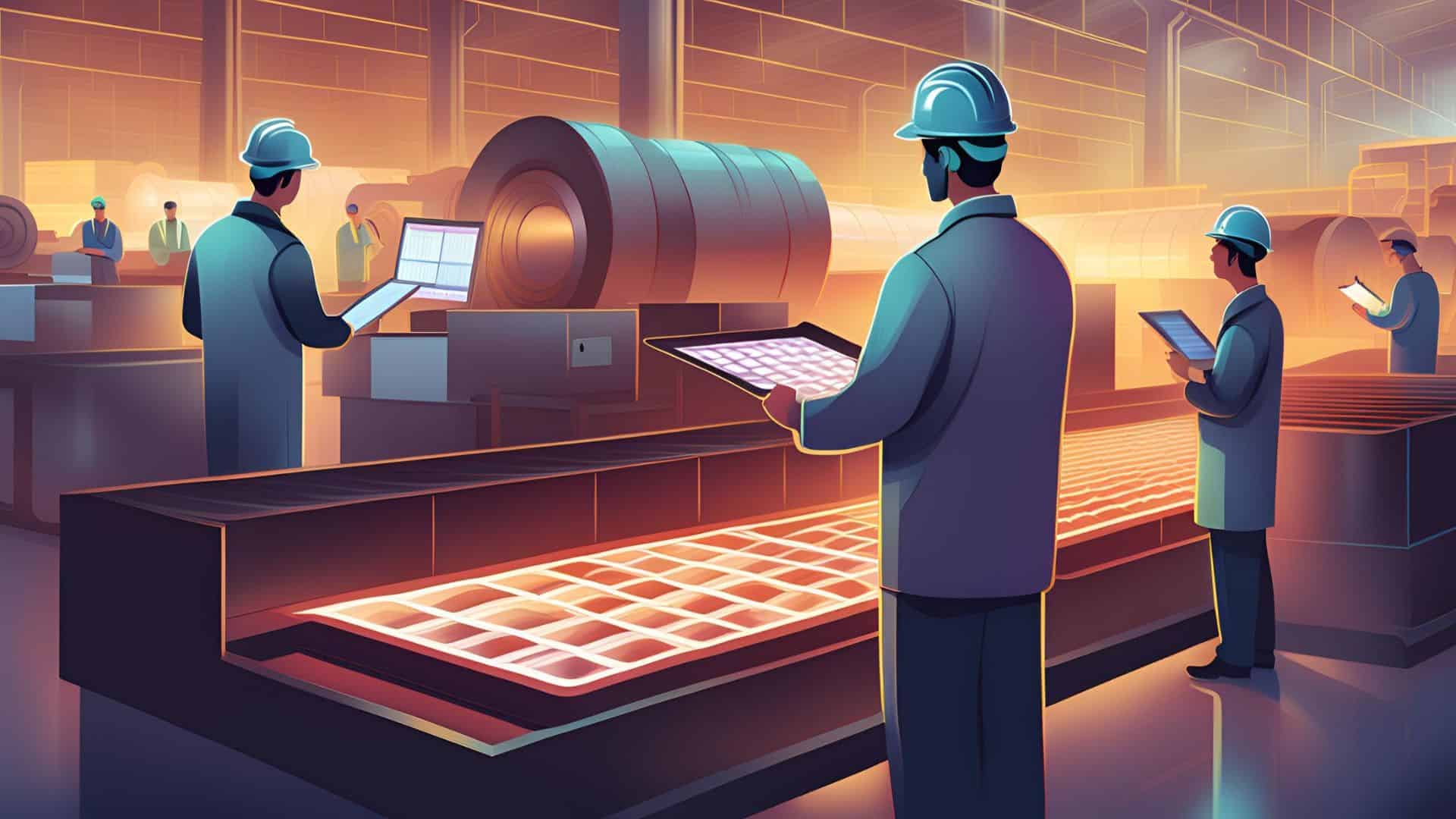
Once you’ve identified where to check, the next step is clarifying what to check for.
Start by outlining specific criteria at each checkpoint. This could include:
- Dimensions and tolerances
- Torque or pressure settings
- Visual quality thresholds
Document these standards in a format everyone can follow — digital work instructions, laminated cards, or integrated checklists in your MES.
When everyone is working from the same quality benchmarks, you reduce confusion and variability.
For more on UK-recognised quality control principles and standards, the BSI Quality Management resource offers helpful guidance.
Step 3: Build Feedback Loops
Into Your Quality Control System
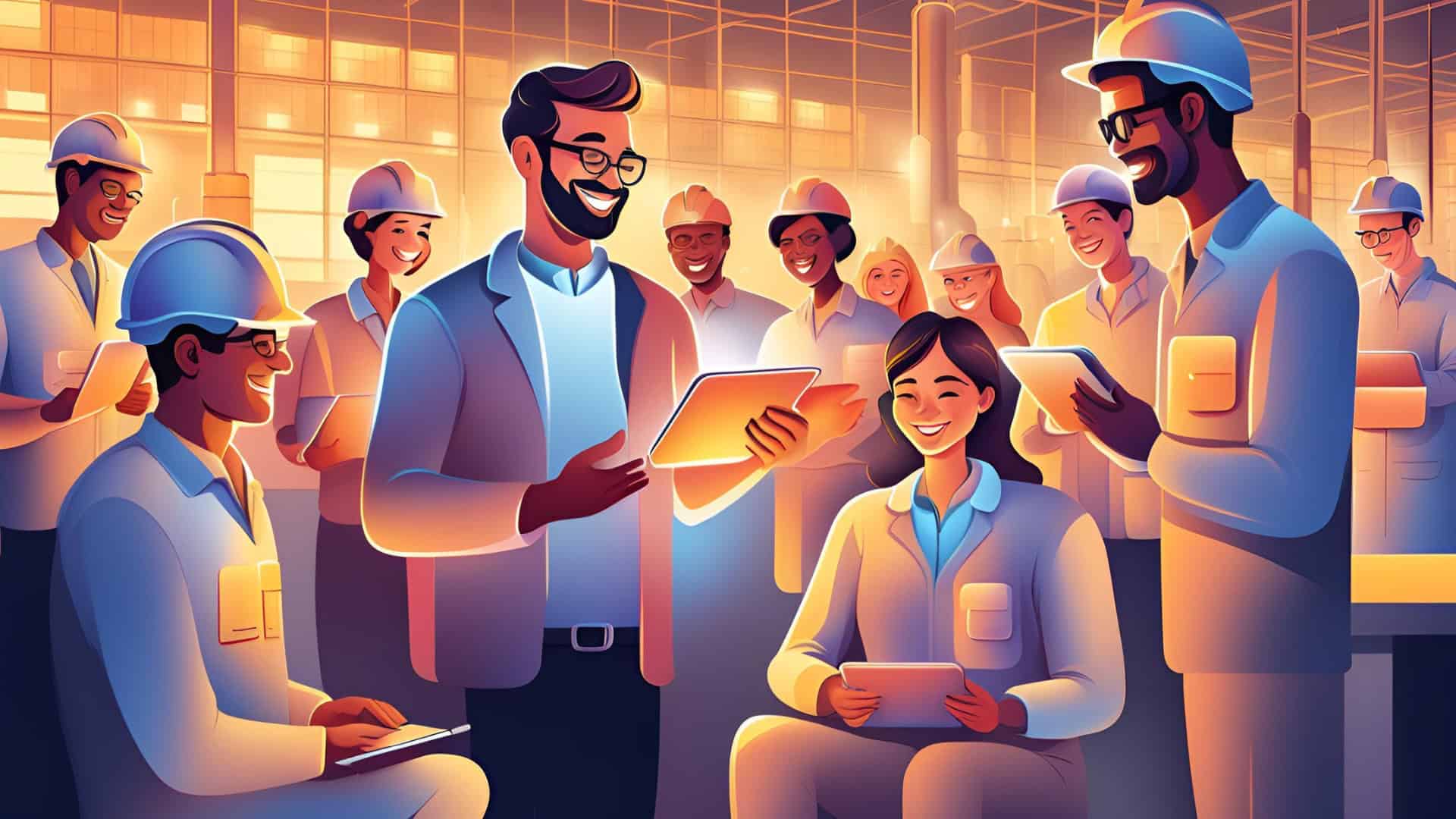
Quality control isn’t static.
What works today might not work next quarter.
Make it easy for your operators to flag issues, suggest improvements, or raise questions in real time. Digital quality checklists or in-process feedback buttons- like those built into Tascus Quality Checks — are effective ways to capture frontline insight.
But it only works if the feedback gets acted on. Set up regular reviews of flagged issues and communicate back what was changed. This creates a culture of continuous improvement and shows your team their input matters.
To see how Six Sigma supports ongoing improvements, this guide from iSixSigma breaks down the DMAIC method used in manufacturing.
Download the Smart Factory Blueprint to start simplifying and enhancing your manufacturing operations with practical tools and insights.
Step 4: Train and Empower Your Team
to Support Quality Control in Manufacturing
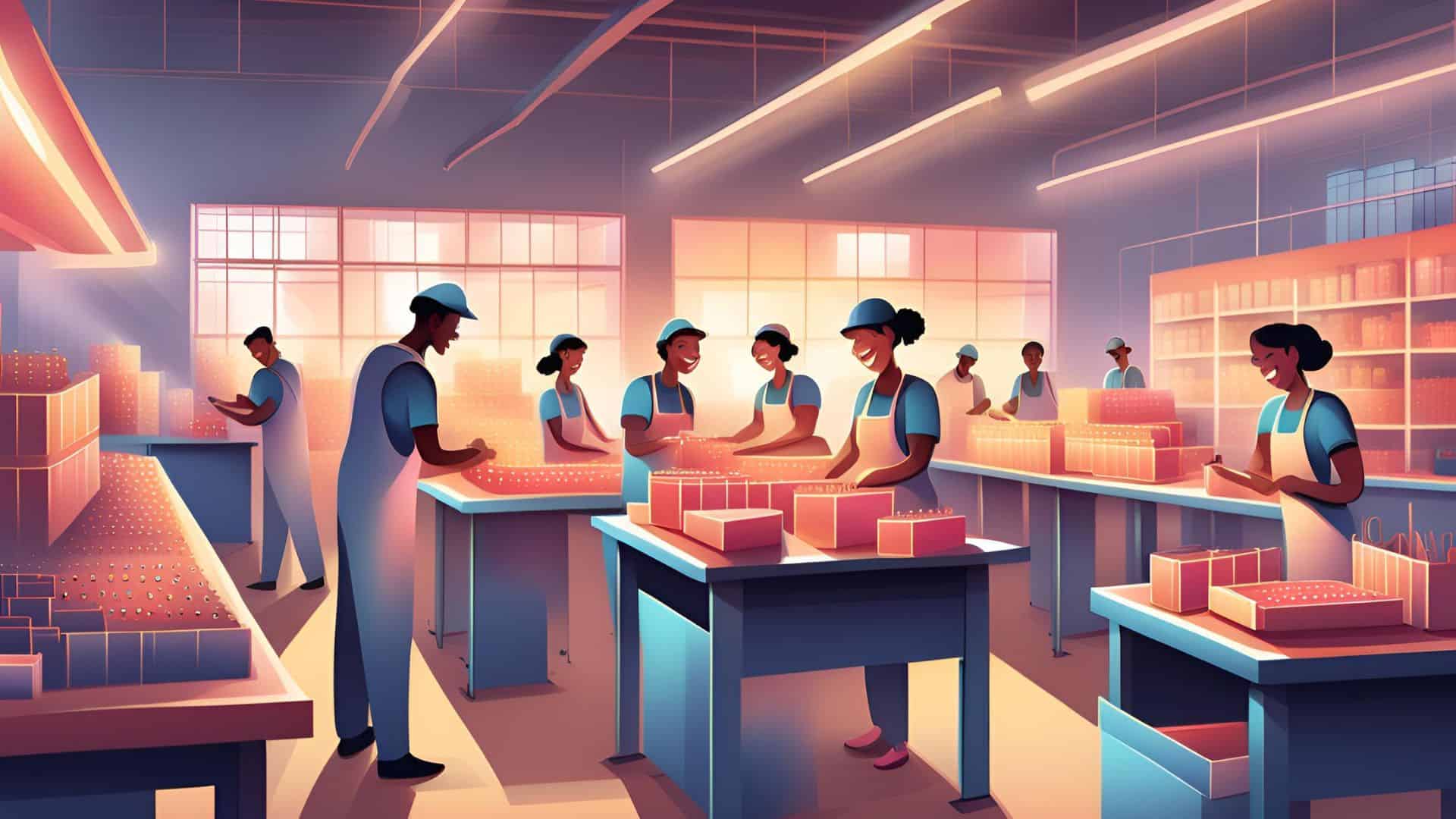
No system will work without people who understand it and believe in it.
To make this effective, ensure everyone is trained on:
✔ Why quality control matters
✔ What their role is in maintaining it
✔ How to complete checks and report issues
Refresher sessions are just as important as onboarding. Processes evolve, and your team needs to stay aligned. When operators understand their impact on the final product, they take more ownership and pride in their work.
What Happens When You Get Quality Control Right?
A strong quality control system built into your workflow brings measurable benefits:
✔ Fewer defects and less rework
✔ Consistent product standards across shifts and teams
✔ Faster audits with digital records and traceability
✔ Scalable production without sacrificing quality
Want to make this your factory’s reality?
Tascus Quality Checks help you catch issues early, maintain consistency, and build in traceability — all without slowing your operators down.
📢 What’s Next?
Embedding quality control is a powerful way to reduce defects, improve efficiency, and build customer trust—but it’s only part of the bigger picture. The next step in optimising your manufacturing processes is data-driven decision-making.
In our next post, we’ll explore Step 3: Analyse, where we’ll break down how to:
✔ Leverage real-time data to track performance and identify inefficiencies.
✔ Use analytics to make smarter, faster decisions.
✔ Optimise production based on key insights, ensuring continuous improvement.
Stay tuned for actionable strategies that will take your manufacturing efficiency to the next level! 🚀
Let’s Talk Tascus
Want to see how Tascus can cut errors,
speed up production, and simplify
compliance in your factory?