Reducing Variation in your Manufacturing Process
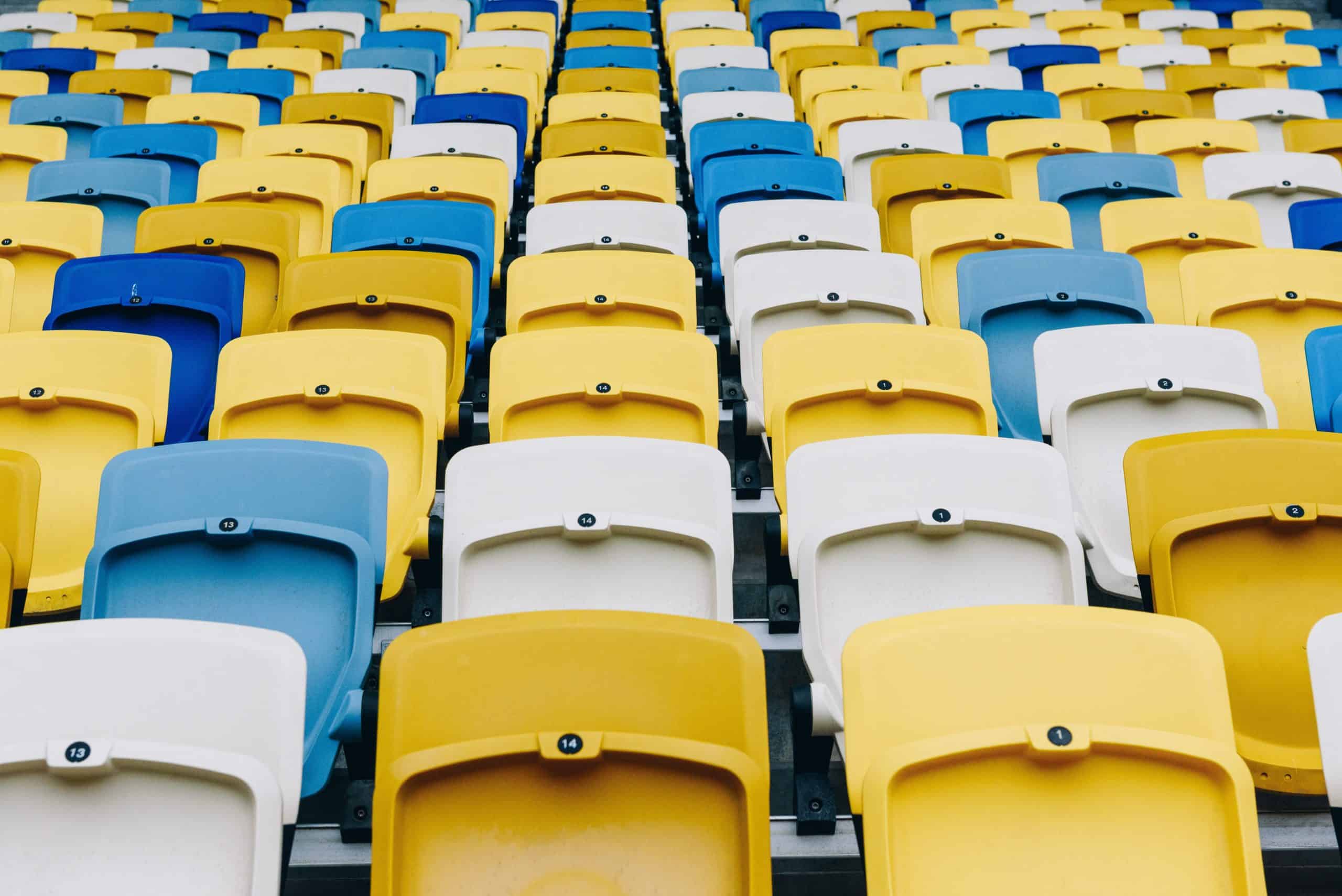
Control is an imperative part of any manufacturing process, and reducing variation is a big step in ensuring control. Why? Because variation is a clear indicator that your manufacturing process is out of control. A high-quality process means the difference between delivering a good or bad product. And if you do end up stopping the process in its tracks before a potentially bad delivery, it could mean double the work, resulting in double the expenses.
The bottom line is this: Reducing variation is a big first step in improving the quality of manufacturing processes – from quantifying the effects, to looking at the process itself, and more. We have five easy-to-follow steps at your disposal for you to learn how to reduce variation and deliver excellent products. Be sure to watch the video below to get the scoop on these five steps!
Quantify Effects
You need to quantify what the effects are as a result of the variation. For example, if bad products are getting through to your customers and having to be returned, what’s the cost of that? What’s the value of that? Is it in the cost of the rework?
You need to understand these costs so that when you embark on a project to reduce the variation, which will have costs itself and consequences in the manufacturing process, you’ ‘ll have something to justify the return on investment from the project.
Materials
Materials coming into the factory is often the number one cause of variation in your manufacturing process.
So, firstly you need to determine if your material suppliers are subject to strict quality controls and inspections. Secondly, if you have multiple suppliers, are the quality and consistency of the materials coming from both suppliers the same?
Investigate this and check that you are getting consistent materials. That’s going to be key to ensuring you get good quality out of your manufacturing process.
Process
Do you have a standard repeatable manufacturing process with fixed, identified stages and gates for everything to go through?
For example, does what happened today on the day shift and tomorrow on the night shift, go through the same process?
Ensuring that this happens is key to getting consistent and low variation products out of your factory.
Measurements
You need to identify some measurements that will be signifiers of low variation in your products. This could be measuring diameters, sizes, electrical measurements, surface finishes etc.
What are the key measurements that you could take during the process to signify whether your processes under control or not? This is called statistical process control (SPC).
If you trend the performance within an upper and lower limit and see the trend go towards one of the extremes, you know that something’s happening to push the process in that direction. It’s a trigger to do something about it. So taking measurements is key to understand how well you’re doing.
Monitor
You may have lots of detailed measurements, but identifying a few high-level KPIs will help you identify key trends in your manufacturing process. This will tell you whether you’re on track to a low variation.
It might be the results of the functional tests at the end of your production line, or a key measurement of the materials coming in. Make sure you identify two or three things which you think have the biggest impact. Track those over time and that will tell you if what you are implementing is putting you on track to improvement.
Summary
So the five steps for reducing the variation in your manufacturing process are:
- Quantify what the variation is costing you at the moment, in terms of either time and money.
- Look at the materials coming into your factory.
- Establish a standard process where everything goes through in the same way.
- Start taking measurements to check if things are of low variation.
- Establish some key KPIs to help you monitor and report how well your process is doing.
Unleash the Power of Digital Manufacturing
Download our free Digital Transformation Starter Kit to set the gold standard for operational clarity and excellence.