How to Implement Traceability in Manufacturing
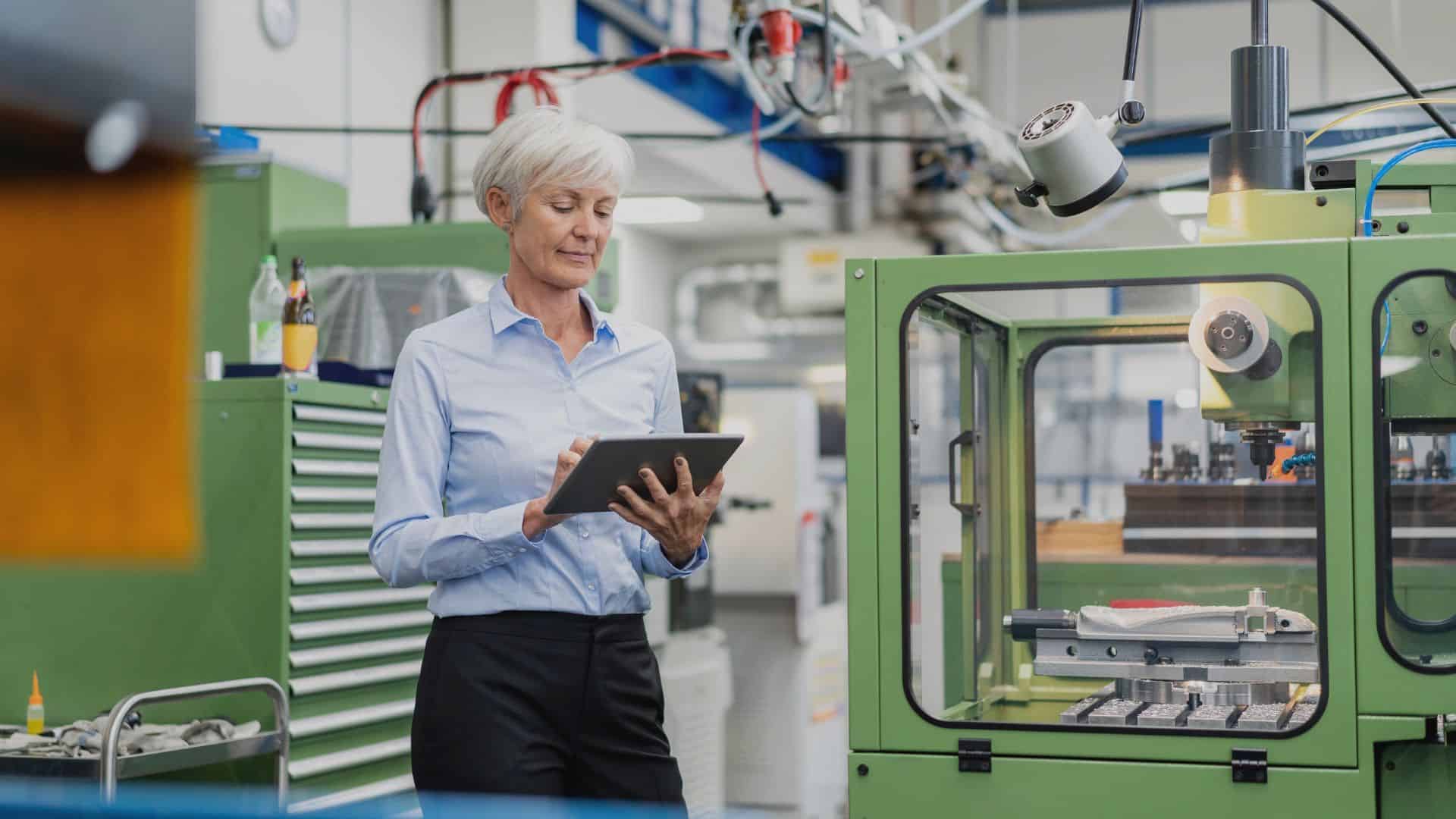
In the rapidly evolving manufacturing industry, traceability has become a critical component for ensuring quality, compliance, and efficiency. Implementing a robust traceability system allows manufacturers to track the entire lifecycle of a product, from raw materials to finished goods.
This capability not only enhances product quality and safety but also improves operational efficiency and customer satisfaction.
Here’s how you can implement traceability in your manufacturing processes effectively.
Start Your
Traceability Transformation
Download the Smart Factory Blueprint to initiate effective traceability across your manufacturing operations.
Define Your Traceability Goals
Establish clear objectives for what you want to achieve with traceability. Whether it’s regulatory compliance, quality assurance, or improving supply chain transparency, having well-defined goals will guide the implementation process. Identify the key metrics and data points that need to be tracked to meet these objectives.
Set Clear
Traceability Objectives
Use the Smart Factory Blueprint to clearly define traceability goals and pinpoint essential metrics for success.
Map Out the Production Process
Create a detailed map of your entire production process, from the sourcing of raw materials to the delivery of finished products. Identify critical control points where data should be collected. This mapping helps in understanding the flow of materials and products, making it easier to pinpoint where traceability measures need to be implemented.
Implement Unique Identification Methods
Assign unique identifiers to each product and its components. This can be done using barcodes, QR codes, RFID tags, or serial numbers. These identifiers should be consistently used throughout the production and supply chain processes to ensure that each item can be accurately tracked at every stage.
Establish Product Identification
Apply the Smart Factory Blueprint to integrate advanced tracking methods like barcodes and RFID tags.
Leverage a Digital Manufacturing Execution System (MES)
Utilise a digital Manufacturing Execution System (MES) like Tascus to streamline the traceability process. An MES can automatically capture and store real-time data from various production stages, reducing the risk of human error and ensuring accurate record-keeping. It provides a centralised platform for managing traceability data, making it easier to access and analyse information when needed.
Train Your Workforce
Ensure that all employees involved in the production process are trained on the importance of traceability and how to use the traceability tools and systems in place. Continuous training and awareness programs can help maintain high standards of data accuracy and compliance, contributing to the overall effectiveness of the traceability system.
Empower Your Team
Utilise the Smart Factory Blueprint to enhance workforce skills in traceability, driving compliance and accuracy.
Final Thoughts
Implementing traceability in manufacturing is a strategic initiative that can greatly enhance product quality, compliance, and operational efficiency. By defining clear goals, mapping the production process, using unique identifiers, leveraging a digital MES, and training the workforce, manufacturers can establish a robust traceability system. This not only ensures regulatory compliance and quality assurance but also builds trust with customers and partners, driving long-term business success.
Let’s Talk Tascus
Want to see how Tascus can cut errors,
speed up production, and simplify
compliance in your factory?